Pharmaceutical Quality Compliance In 2022: Data Is Paramount
By Shahid Manzur, EY
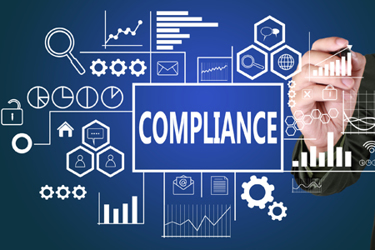
The urgent need to respond to the COVID-19 pandemic with therapeutics and vaccines compressed pharma’s go-to-market timeline. But while urgent public health needs accelerated focus on production, the industry’s rigorous and often manual compliance protocols are placing unique pressures on pharma manufacturing and quality teams.
Pharma quality and compliance leaders must anticipate potential manufacturing issues before they happen by leveraging risk-based methodologies, continuously monitoring their systems, and tracking the profusion of data generated during the process. But while the transforming promise of better analytics in pharma manufacturing is clear, creating genuine insights capable of supporting real-world decisions remains difficult. Making meaningful improvements to complex manufacturing processes requires reliable insights while keeping pace with accelerated production demands.
This piece outlines resources that have the potential to allow compliance leaders to improve quality performance — and get their production team’s culture in step with this new normal.
An Overview Of Pharma Quality Today
When vaccine production ramped up in 2021 to meet President Biden’s call for national vaccine availability, pharma manufacturing quality was closely scrutinized. The industry was exposed to significant economic and societal penalties as it undertook an unprecedented vaccine production effort. And when a quality issue at a contract manufacturing facility resulted in the contamination of as many as 15 million vaccine doses, the ensuing media, government, and public outcry demonstrated the high stakes of modern pharma manufacturing.
In 2022, pharma quality teams face internal and external obstacles in their searches for efficiencies in production. The industry-wide norm of disparate manufacturing execution systems, enterprise resource planning, lab, and quality management systems complicate internal processes. Communication channels with contract manufacturers lack the reliability needed for timely insights and deep collaboration, while over-reliance on manual processes and data exchanges impact performance and make manufacturers vulnerable to data integrity-related problems.
A rapidly evolving regulatory landscape calls for added agility and the ability to proactively adapt to new requirements, but vulnerable relationships and lack of tools to support effective investigations prevent quality teams from setting production plans and addressing recurring errors.
The Potential Of Data And Analytics To Support Quality
Great opportunity for pharma exists alongside those challenges, as the potential for data to monitor quality performance is vast and largely untapped. Advanced analytics promote better decisions across operations and the supply chain today, and manufacturers can anticipate problems before they arise.
Pharma manufacturers can harness a significant amount of available data from labs, shop floors, logistics providers, and distribution networks. Insights from these data sets make real-time monitoring possible to improve quality performance and promptly address quality incidents. Data can help identify systemic issues, provide insights into aging quality records, identify bottlenecks, and deliver right-first-time results. Clustering and data mining techniques can identify systemic root causes, while advanced monitoring techniques provide early signal detection and effectively investigate customer complaints. Past quality performance can be used to predict completion times for CAPAs, and automation techniques can help significantly reduce cycle times for batch disposition.
With next-generation cell and gene therapies, a significant amount of data is collected at the point of care and throughout the process. This presents a significant opportunity for proactive monitoring to avoid potential quality issues in the end-to-end life cycle. From site activation, patient enrollment, and apheresis to manufacturing process, quality review, and product release, hundreds of data points are collected that can offer insights into manufacturing and quality performance.
However, pharma quality control also faces new challenges. Personalized micro batch pharmaceuticals require careful attention to the minute details of a complex manufacturing procedure. As these therapies continue to mature and grow more common, the need to integrate quality performance with safety and pharmacovigilance information to provide a comprehensive view throughout the complete therapy life cycle will increase.
The New Pharma Manufacturing Approach
Traditionally, quality teams have focused on managing quality-related events, supporting inspections, and conducting regulatory and retrospective management reporting. In the future, there will be an ever-increasing need for greater collaboration between quality and broader operations.
Integrating multiple data sets and drawing data information from a variety of systems — including quality management systems, enterprise resource planning, manufacturing execution systems, and laboratory information management systems — can unlock powerful insights and improve audit preparedness. When investigating product complaints, quality teams need to review where the product was manufactured, packaged, and distributed, know current inventory levels, and understand all quality issues associated with the batch and trends across products.
To accelerate greater collaboration between quality and broader operations, quality teams must pivot from retrospective reporting to data-driven techniques. They should seek to provide proactive insights to upstream processes and flag potential issues before they happen. Similarly, manufacturing and supply chain operations can improve planning when they have greater visibility into quality performance. Quality organizations will also focus on automation and find opportunities to reduce cycle times for supporting major processes, including annual product reviews, field alert reporting, and batch disposition related activities.
The spread of the omicron variant – and announcements of omicron-specific vaccines – will keep the spotlight on pharma manufacturing quality in 2022. In this new normal, compliance leaders have a unique opportunity to rethink their approach to quality controls. Using proactive analysis and digitized platforms to investigate and resolve issues can help quality teams make better decisions, support compliance, and drive improvements in performance – ultimately improving patient outcomes.
About The Author:
Shahid Manzur is a principal in the Life Sciences sector at EY, specializing in analytics, planning, forecasting, and decision support for pharmaceutical clients. He has more than 18 years of experience that includes product development and implementations, serving life sciences clients across both technical and commercial operations. Previously, Manzur was a solution architect with SAP Labs, where he led product development for a forecasting application. He holds a BS in computer engineering from Purdue University, and a MS in finance and an MBA in operations from the University of Maryland.
The views expressed by the author are not necessarily those of Ernst & Young LLP or other members of the global EY organization.