ICH Guideline Q9(R1) On QRM, Part 2: Subjectivity & Supply Continuity
By Danica Brown and Theo Zacharatos, ValSource Inc.
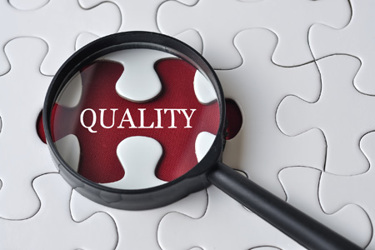
The long-awaited revision to ICH’s harmonized tripartite guidance on Quality Risk Management, Q9(R1), was adopted on January 18 of this year. While the primary principles and concepts detailed by the guidance remain consistent with the original 2005 document, the longer, revised guidance has four new subsections. A previous article reviewed updates to the risk management methodology section to include formality and risk-based decision-making.1 In this article, the added topics of subjectivity and QRM in addressing product availability risks will be considered.
Subjectivity In QRM
Like the other new methodology sections, ICH Q9(R1)’s expanded discussion of subjectivity is an addition that is evolutionary, not revolutionary. Since its initial release, Q9’s first primary principle of quality risk management (QRM) is that evaluation of risk should be based on scientific knowledge. This guiding principle has steered risk assessment teams away from subjectivity since the guidance’s inception and remains unchanged in the adopted revision. In the new revision, decision makers in QRM activities have an additional listed responsibility to ensure that subjectivity is managed and minimized, with the intent of making scientifically robust decisions.
Section 5.3 first acknowledges subjectivity’s pervasive nature, which can influence all parts of the QRM process. The guidance notes various means through which subjectivity may be introduced, including:
- Differences in how risks are assessed
- Differences in how hazards, harms, and risks are seen by various stakeholders
- Inadequately defined risk questions
- Poorly defined risk rating scales
The section acknowledges that subjectivity cannot be eliminated, but its presence can be addressed through properly designed tools and by leveraging available knowledge and data. All QRM participants are instructed to take an active role in being aware of and addressing subjectivity.
What Does This Mean To Firms?
Without managing and minimizing subjectivity, an organization’s QRM exercises will fail to drive consistency in decision-making. As proper design and use of QRM tools can help manage subjectivity in QRM, applying the updated guidance may first prompt a review of tools currently used in a QRM program. Programs with a higher level of maturity may already integrate practices that serve to minimize and address subjectivity. For those looking to reduce potential subjectivity, the design of tools and the definition given to assumptions can be helpful.
The Role Of Risk Scoring Scales In Minimizing Subjectivity
Procedurally defined risk assessment tools provide teams with rating scales and criteria that should help reduce the potential for team or stakeholder subjectivity to influence outcomes. A risk tool’s criteria can act as a driver for consistency among stakeholders and across assessments in an organization by minimizing the opportunity for bias in ratings. When these criteria are little more than a vague rephrasing of the rating itself, they lack the detail needed to instruct teams on how to evaluate information in a consistent way. Instead, scales should include criteria that speak to the questions each tool may be used to assess and the information used in making determinations.
QRM tools should prompt teams to gather and review available knowledge and guide them in interpreting available information to meet Q9’s primary principles. Without criteria that give enough detail to harmonize interpretation, teams may default to the mental shortcuts provided by biases and heuristics. It is common to see teams unduly weight recent data points (availability bias2), rely on how they feel about a given risk (affect heuristic3), or rate based on their mental model of a “typical” system or process (representativeness heuristic4).
The Role Of Assumptions In Managing Subjectivity
The revised Q9 also prompts users to acknowledge assumptions made by the team in the QRM process. Within a risk assessment team, there is often a shared context that guides discussions and decision making. Conversely, the team may be working under uncertainty and using best guesses or models for similarity to inform the risk assessment. Without discussing these assumptions and ensuring alignment among the team, at a minimum, key context is lost in the final risk assessment output. In worse cases, stakeholders may complete the entire assessment while working with different assumptions. Risk assessment teams should ensure that assumptions are defined during the early stages of an assessment and included in their outputs to meet Q9(R1)’s guidance.
While addressing and minimizing opportunities for subjectivity is a familiar topic for many QRM practitioners, the additional guidance and prominence it has in Q9’s revision should prompt users to examine opportunities for subjectivity in their risk assessment processes, including:
- How are risk questions defined and scoped?
- How are teams instructed and guided toward assigning ratings?
- What stakeholder assumptions are made in performing the risk assessment?
- How are potential sources of bias managed?
- How can decision makers demonstrate that they are managing and minimizing subjectivity?
Product Availability Risks
ICH Q9(R1) also includes a new section, 6.1, titled The role of Quality Risk Management in Addressing Product Availability Risks Arising from Quality/Manufacturing Issues. This section focuses on how QRM can support supply continuity. Discussion of risk management for supply continuity and product availability has been top of mind for regulatory agencies and was addressed in FDA’s 2022 guidance on Risk Management Plans to Mitigate the Potential for Drug Shortages. The new section on this topic in Q9(R1) strives to understand system vulnerabilities that may disrupt the ability for lifesaving products to reach intended patients.
Factors highlighted in Q9(R1) that may impact product availability include:
- Process variability
The inability to produce consistent quality product (through process drift or non-uniformity) may lead to lower yields and longer wait times for patients to receive needed quality medication. QRM can help to develop monitoring systems that can identify weaknesses in the manufacturing process.
- Manufacturing facility and equipment
Maintaining a robust facility infrastructure facilitates reliable supply. Infrastructure may become compromised by an aging facility and equipment, insufficient maintenance of the facility, or equipment and poor operational design. It is also important to understand utility system capacities during normal versus surge manufacturing (i.e., is there enough water for injection production to meet product and equipment prep needs?).
- Oversight of outsourced activities and suppliers
Quality system governance assures that supply chain partners are capable of delivering services over the drug product life cycle. An issue with a sole supplier of critical components, raw materials, and intermediates would curtail drug product availability. A third-party outsourced filling operation with an inability to finish drug product labeling will most certainly prevent the final product from reaching the patient. Similar effects may be realized with third-party laboratories. If testing is critical to the release process and the laboratory does not produce reliable results, this will presumably delay the final product from reaching the patient. QRM can help identify weaknesses and develop mitigations for supply chain vulnerabilities and address potential continuity concerns with third-party contract manufacturers.
What Does This Mean To Firms?
- Process variability
QRM can be leveraged to identify the areas producing variability, support development of monitoring programs for critical parameters of the manufacturing process, establish control charts with upper and lower-level limit expectations, and routinely assess process capability. Ideally, real-time data capture will be used to ensure the current process is within the normal processing range. When process drift is observed, QRM can facilitate the required escalations to product/process stakeholders and to take actions tracked through quality system. Management review meetings should be established to routinely review process capability to enable risk communication and ensure stakeholders understand when and how the drift is occurring.
- Manufacturing facility and equipment
QRM can be applied across the facility, ensuring utility systems are robust. Leveraging QRM at the design phase can remove inefficient designs, mitigating risks of human errors. Ideally, if financially feasible, this can be further supported via the use of automation and digitalization across the facility.
To mitigate the effects of an aging facility, a robust maintenance program is critical. QRM risk-based decisions can be created and incorporated into calibration/maintenance procedures to guide engineers to remove subjectivity and create consistent determination of equipment classification and frequency of maintenance.
Real-time automated monitoring programs must be established to ensure facility systems are performing as intended. A detailed review of facility systems can occur through QRM tools to ensure holistic capture of all required monitoring.
- Oversight of outsourced activities and suppliers
QRM can be leveraged to develop a monitoring program for product quality parameters of a supplier and contract manufacturing organization (CMO). The monitoring should have criticality scales developed by stakeholders included in procedures, along with the action to be taken if overall risk thresholds are achieved. The intent is to remove subjectivity by creating a criticality scale and placing risk-based decisions within a procedure to ensure stakeholders act consistently. A Material Review Board composed of product stakeholders should routinely review data. If product quality is drifting, communication should be established with the supplier/CMO, with clear expectations and a means of collaboration.
Use of QRM can help to identify weaknesses and reduce the risk of a drug product shortage if a critical supplier cannot provide a component, API, or intermediate. Risk mitigations can be used to increase inventories or qualify secondary suppliers. If possible, identify like-for-like components used by sister sites in the event a request for an item is required.
Throughout a product’s life cycle, deviations that could impact the product should also be examined for the potential to pose a supply continuity risk. A QRM tool should be developed for each deviation that has impact on the product, guiding those classifying the deviation to consistently account for inventory levels and market demand to identify supply continuity risk. If inventory is low and market demand will exceed inventory, the deviation must take priority, and the supply chain disruption must be communicated to stakeholders. Ensuring proper impact assessment is critical with a risk-based impact assessment.
Conclusion
Updates to the methodology and integration sections in Q9(R1) provide clarity to leadership and practitioners alike on subjectivity and QRM for product supply. Beyond the expectation to implement the ICH guidance, managing subjectivity and reducing the risk of product shortage both benefit the overall health of a company’s product quality.
Between these updates and those in the formality and risk-based decision-making sections, the new guidance can prompt a review of relevant tools and processes within an organization. For those with a baseline level of QRM maturity, next steps may include implementing use of trained facilitators to lead risk assessments, diversifying the risk tools used internally, and integrating proactive QRM elements into the quality system. Given the current regulatory focus on the use of risk management principles, their appropriate use and implementation will continue to be a topic of interest in ongoing industry discussions.
References
- https://www.outsourcedpharma.com/doc/ich-guideline-q-r-on-qrm-part-formality-risk-based-decisions-0001
- Tversky, A.; Kahneman, D. (1974). "Judgment under Uncertainty: Heuristics and Biases". Science. 185 (4157): 1124–1131.
- Finucane, M.L.; Alhakami, A.; Slovic, P.; Johnson, S.M. (January 2000). "The Affect Heuristic in Judgment of Risks and Benefits". Journal of Behavioral Decision Making
- Kahneman, Daniel; Tversky, Amos (1972). "Subjective probability: A judgment of representativeness". Cognitive Psychology. 3 (3): 430–45
About The Authors:
Danica Brown is a consultant with ValSource, Inc., with expertise in the development and deployment of customized solutions to QRM, including program design, development of risk-based approaches, and integration of QRM within quality systems. Her expertise also spans quality functions in the pharmaceutical, biopharmaceutical, and medical device industries, including quality strategy and process improvements, deviations/investigations, and design verification and validation. She has a B.S. in biochemistry from Simmons College and an MBA from the University of Massachusetts. Brown is an ASQ Certified Quality Engineer and Lean Six Sigma Green Belt, and is an active member with PDA and a participant on its Knowledge Management task force. She can be reached at dbrown@valsource.com.
Theo Zacharatos is a ValSource consultant with over 20 years’ experience in a variety of quality and engineering roles. He has extensive experience within quality, spanning quality risk management, aseptic processing, fill/finish, deviation/CAPA management, process trending, and final product release. Prior to his work with ValSource, Zacharatos incorporated risk-based decision-making across multiple quality systems. He has a B.S. in chemistry and a B.E. in chemical engineering from New York University and Stevens Institute of Technology. He can be reached at tzacharatos@valsource.com.